Spring into Safety with Fleet Repair and Maintenance
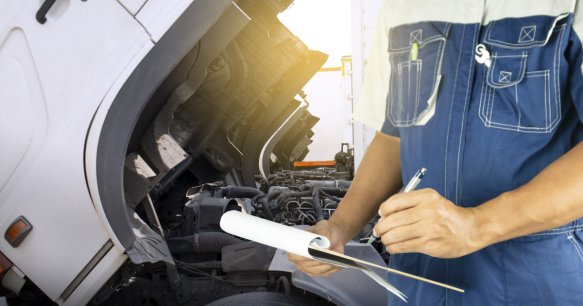
With any change in season comes a need to ensure that your fleet is in optimal condition, ready to face the busy months that lie ahead. Spring is no exception. After months of storage or minimal use, it’s essential to provide your Portable Traffic Signals and Automated Flagger Assistance Devices (AFADs) with some well-deserved maintenance, ensuring smooth operations on your road construction sites. In today’s blog, we’ll highlight the importance of spring maintenance while providing several pro-tips to prepare your North America Traffic control systems for the upcoming season.
Why Spring Maintenance Matters
As the possibility of increased operational demands surfaces, a detailed examination of your fleet becomes vital to ensuring its overall success. Consider it a proactive investment in the longevity and reliability of your assets. It’s not just about addressing existing issues but reinforcing your equipment to withstand the challenges ahead. By identifying and resolving potential issues before they escalate, spring maintenance defends against unforeseen breakdowns, reducing downtime and ensuring that your fleet remains a reliable and effective asset throughout your most demanding seasons.
When it comes to traffic control systems, setting time aside to practice spring maintenance is especially important. Similar to spring maintenance as a whole, routinely preserving Portable Traffic Signals and AFADs can mitigate the potential for disruptions and optimize the overall efficiency of your fleet. This seasonal maintenance not only protects your equipment but also enhances the safety of your operations, protecting workers, motorists, and pedestrians. This commitment to safety, in turn, positively impacts your organization’s reputation, painting you as a company dedicated to the highest industry standards.
Spring Maintenance Tips for Your Portable Traffic Signals and AFADs
Although spring maintenance looks different from industry to industry, some tasks are universal. Below we outline several tasks, along with some tips, to help you prepare your Portable Traffic Signals and/or Automated Flagger Assistance Devices for the upcoming season.
Thoroughly Inspect Tires
- Assess Tread Depth. Evaluate the tread depth of your tires to ensure you have enough traction to grip the road. The penny/quarter test is a great way to do this. Simply place a penny or quarter upside down in your tread, and if you can see the top of the coin’s head, it’s likely time to invest in some new tires.
- Ensure Appropriate Tire Pressure. Using a pressure gauge, make sure your tires are properly inflated. Fill with air as needed. To check for pressure, remove the valve stem cap and using firm pressure, remove the gauge and read the pressure. Compare the following recommended inflation pressures to your tire’s readings:
- RCF2.4: 50 psi
- RCF3.4: 50 psi
- PTL2.4x: 50 psi
- PTL2.4LD: 50 psi
- Consider Tire Condition and Age. Inspect the tread and sidewalls for cuts, scrapes, punctures, bulges, bumps, and/or cracks. Don’t forget to be mindful of your tire’s age. To determine their age, look at the DOT stamping on the sidewall. At the end of the DOT stamping, there will be a 4-digit number, known as the data code. The first two numbers indicate the week it was manufactured, with the last two demonstrating the year. For example, the number 3019 would reveal that the tire was made in the 30th week of 2019.
- Ensure Proper Torque of Lug Nuts. After 10, 25, and 50 miles on the road, and every subsequent month thereafter, it’s important to ensure the proper torque of lug nuts. Depending on your NAT traffic control solution, the torque pressure should be as follows:
- RCF2.4: 60 ft/lbs.
- RCF3.4: 60 ft/lbs.
- PTL2.4x: 120 ft/lbs.
- PTL2.4LD: 120 ft/lbs.
- Check Axle Grease. How often you grease your wheel bearings depends on the trailer size. Regularly inspect the quality of grease within the hub cap. There is no disassembly required. Below are the steps to replace axle grease:
- Jack the trailer up to lift the wheels.
- Remove the rubber plug from the end of the grease cap.
- Place a standard manual grease gun on the grease fitting.
- While rotating the wheel, slowly pump grease into the fitting. The old, displaced grease will flow out of the cap, around the grease gun nozzle. When clean grease is observed, remove the grease gun, wipe off excess and replace the rubber plug on the grease cap.
- Examine Axle Bolts for Proper Torque. This next one should be done monthly, along with torquing of the lug nuts on the tires. The torque pressure should be as follows depending on your NAT traffic control solution:
- RCF2.4: 90 ft/lbs.
- RCF3.4: 90 ft/lbs.
- PTL2.4x: 150 ft/lbs.
- PTL2.4LD: 120 ft/lbs.
Fully Assess Trailer Components
- Look Over Tongue Hitch Coupler. Routinely check and ensure that the tongue hitch coupler is torqued to 45 ft/lbs.
- Analyze Hitch Coupler Components. First, ensure the latch has a full range of motion. Then, confirm the coupler locks on the ball without any movement or play. Next, tighten the adjusting nut, as required. Check out this YouTube Video for a great how-to. Finally, inspect the underjaw for any wear or damage.
- Inspect All Locking Pins for Excessive Wear or Damage
- Review the Tongue/Draw Bar for Any Signs of Damage
- Test the Running Lights for Proper Function. Connect the trailer to your towing vehicle and connect the running light plug to test.
Maintenance Logs and Inventory Appraisal
Anytime maintenance is done, it’s essential to keep detailed records. Whether you update current maintenance logs or start a new record-keeping practice, the choice is yours, just make sure to keep an up-to-date record containing the machine’s technical details and the steps taken to ensure its optimal condition. For example, include information such as the model number, hours of service, filter type, oil grade, part identifiers, dates of greasing parts, oil changes, and if applicable, repair history.
Maintenance logs also present you with the opportunity to evaluate your inventory, ensuring you’re well-equipped to handle the upcoming season. Consider if there are any machines part of your fleet that are currently in need of replacement or if any necessary additions are required to enhance the functionality of your task force.
Take Stock of Paperwork
Being aware of when your professional licenses are set to expire in the forthcoming year is imperative. It’s also not a bad idea to review your warranty requirements and insurance policies, ensuring you thoroughly understand the conditions.
This routine check ensures that your paperwork is in order, aligning with industry standards and safeguarding your operational processes. Keeping well-informed of license renewals and understanding warranty and insurance details forms an integral part of maintaining compliance and mitigating potential risks in your operations.
Fleet Vehicle Inspection Checklist
Once repairs and maintenance are completed, complete an overall inspection of your vehicles to uncover any issues that may have taken shape over the winter, such as broken wires or leaks. Here are some key components to examine:
- Visibility and Signalling Components: Evaluate the functionality of lights and flashers. These components play a critical role in conveying information and include everything from your portable traffic signals to the lights on your truck.
- Equipment Hoses, Clamps, and Seals: Carefully inspect for any sign of wear, leaks or other potential issues that could wreak havoc down the road.
- Tires: Tires serve as the foundation of your fleet. Meticulously check tire pressure, tread depth, and overall condition. Rotate tires as necessary to promote even wear and extend life.
- Gate Arm: Thoroughly examine the gate arm on your portable traffic signals and AFADs. Check for any signs of damage or wear.
- Battery: Inspect the battery, confirming its charge and overall condition. Provided the potential impact harsh winter weather can have on batteries, this step is essential in preventing unexpected breakdowns. To ensure the peak performance of your NAT Portable Traffic Signals this spring, watch our how-to video on effective battery maintenance for both our PTL and AFAD units. View the video here.
- Required Stickers and Decals: These are essential for conveying important information. Routinely check and maintain these stickers and decals to ensure compliance and effective communication.
This fleet vehicle inspection checklist works to not only address immediate concerns but also serve as a proactive measure to uphold the safety, reliability, and overall efficiency of your fleet.
Routine checks of these critical components contribute to a well-maintained fleet, minimizing the risk of unexpected issues and enhancing the overall longevity of your vehicles.
Prepare Your Fleet for the Upcoming Season with NAT
As you gear up for the busy season, investing time in spring maintenance for your Portable Traffic Signals, AFADs and other essential equipment is a smart choice. North America Traffic is positioned to support your traffic control requirements, providing reliable products such as the RCF2.4 Automated Flagger Assistance Device and cutting-edge Portable Traffic Signals.
Contact us today to explore how we can elevate the safety and efficiency of your road construction sites. Spring into safety with NAT– your trusted partner in traffic solutions!